By Lindsey Coulter
As architects and construction professionals look to 2025, the year’s most exciting industry trend might just be…wood. More specifically, engineered wood products and mass timber are opening new doors and design possibilities, allowing forward-thinking project teams to build more efficiently and sustainably across a number of verticals.
The mass timber trend began in Austria and Germany in the 1990s and first caught on in the U.S. in the lumber-rich Pacific Northwest. The region, which also hosts the annual Mass Timber Conference, remains home to the majority of the country’s mass timber buildings, but the product is gaining a foothold across the country. Driven largely by advocate Peter MacKeith, dean of the Fay Jones School of Architecture and Design at the University of Arkansas, the state is also becoming a mass timber driver (the University also hosts the annual Arkansas Mass Timber Conference). Meanwhile, Michigan’s updated building codes, which take effect April 9, will include three new mass timber building types (the previous code allowed for just one type) and will allow projects of up to 18 stories.
National construction firm Swinerton Builders has become an enthusiastic proponent of mass timber as a sustainable, versatile, and efficient construction material that supports regional economies, reduces carbon emissions, and offers numerous aesthetic and biophilic benefits. The company has developed more than 60 mass timber projects since 2018 that—when compared to more traditional steel and concrete structures—reduce carbon emissions, save money, reduce construction time and achieve a more natural aesthetic.
Product Types and Terminology
William Silva, Pacific Northwest Regional director of preconstruction for Swinerton Builders, is eager to share the company’s mass timber work. Swinerton’s first mass timber project—the First Tech Federal Credit Union Oregon Corporate Campus in 2016—was then the largest mass timber office building in the U.S. The project was notably delivered four months faster and four percent cheaper than had it used structural steel. More recent projects include Northlake Commons, which through the utilization of mass timber avoided an estimated 1,990 metric tons of CO2e (carbon dioxide equivalent) emissions, or the equivalent to removing 558 cars from the road.
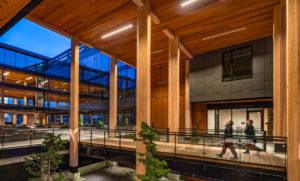
While earlier one-way iterations of mass timber—such as mechanically laminated timber (nail-laminated or dowel-laminated), glue-laminated timber (or glu-lam), and laminated veneer lumber—are common in columns and beams, Silva saw construction possibilities take off with the integration of one-way products with two-way assemblies such as cross-laminated timber and mass plywood panels.
“What’s really exciting is the dimensional certainty; we’re able to build and fabricate projects using mass timber that are accurate to 1/16 of an inch,” Silva said.
In addition to understanding the various products available, Silva also helps clients understand the difference between manufacturing—the process of pressing lumber pieces into a beam product—and fabrication, which processes the wood beam, sizing it and preparing it for hardware installation in a specific project.
“When discussing mass timber projects, we started to move from the term ‘building’ to ‘assembling’ just to change people’s mindset,” Silva said. “We assemble the prepared mass timber elements into the components of the building.”
Marrying the mass timber product with virtual design and construction technologies and building information modeling, creating a digital twin of a project, also allows clients to better understand the product’s possibilities—and helps project teams anticipate needs and challenges before construction.
“Construction is based on habits, customs and beliefs that are based in 13th century trade guilds,” Silva said. “The industry really hasn’t evolved as rapidly as other industries have. And so, to me, (mass timber) is an opportunity to really advance how projects get delivered and to rethink how… teams can collaborate and how that all integrates into how we deliver the built environment.”
Cost and Value Considerations
The benefits of mass timber often overlap. The product is best-known for its sustainability, energy- and carbon-reduction properties and aesthetic appeal—as well as its structural and schedule efficiency. However, using mass timber products can also help projects proceed despite systemic labor shortages across the construction industry, and helps creates living-wage fabrication jobs.
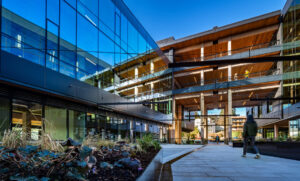
“Prefabrication and dimensional certainty allow project teams to operate in a much more efficient way. You really need just a 6- to 7-person crew to assemble the building on the site,” Silva said.
This reduced workforce, and the fact that beams and components are fabricated offsite, makes jobsites much quieter and less disruptive to their communities. Mass timber projects are also generally built faster and more economically than structural steel facilities, as they lend themselves to a more integrated approach to project delivery.
“Whenever somebody tries to make mass timber do what concrete or steel does, it usually isn’t successful,” Silva said. “It’s really about understanding and building with the product’s strengths. We’ve done 18-foot cantilevers with a mass timber structure. If you understand the strengths and you work with the right design team you can, through innovation, do exciting things that you couldn’t do with concrete and steel.”
Thus far Swinerton’s tallest mass timber project is 19 stories, and Silva notes that the product is particularly adaptable for tight, urban sites with narrow access and other constraints. The company is also creating a tool to help teams choose products and design approaches based on advantages, teasing out specific opportunities available in mass timber for each unique project depending on time, location and other factors.
Renewability and Sustainability
For a recent 156,000-square-foot commercial project, owners were particularly excited about the surprisingly low impact of their facility, as Swinerton calculated that Oregon forests could regrow all the wood used in the mass-timber project in just 46 minutes.
“If you apply that to all of North American forests, it would take just 14 minutes,” Silva added.
This has also spurred conversations about mass timber’s sequestered and embodied carbon story as well as forest management practices, transparency, sourcing, and ensuring social equity opportunities by working with rural and tribal partners.
Read more about the mass timber trend and other notable mass timber projects in the upcoming January/February edition of Green Building News’ sister publication School Construction News.